Automated Vacuum Cure Systems
YES pioneered the use of vacuum curing, and has continued to perfect and patent the many innovations required to provide YES customers with superior film performance at twice the speed and half the cost of ownership of conventional cure technology. The VertaCure PLP is the result of the company’s decades of experience, and large semiconductor manufacturers depend upon it for high reliability, cost-effective production.
VertaCure PLP is a fully automated vacuum curing system that provides complete removal of residual solvents, uniform temperature distribution, complete imidization, and precise management of heating and cooling rates. Benefits include no outgassing after cure, better thermal, mechanical and electrical properties, and excellent particle performance.
The VertaCure system is available with one or two modules, for processing 12 or 24 panels in a single run. It accommodates panel sizes from 400 mm to 550 mm, with automated loading and unloading via EFEM.
Applications include polyimide/PBO cure, D2P bonding, low-temperature cure and pre-metal degas.
Production-proven Excellence
Utilizing YES’s patented vacuum cure process, the VertaCure PLP offers shorter cure time, excellent temperature uniformity and high uptime for high volume manufacturing (HVM).
Chamber Exhaust Condensate Trap
Protect vacuum lines, valves, and vacuum pump performance from the accumulation of solvent condensates during the cure process. Easily dispose of the condensates.
Laminar Flow Technology
The VertaCure PLP ensures laminar flow of gas (parallel to the panels) to eliminate gas turbulence, resulting in excellent temperature uniformity and industry-leading particle performance.
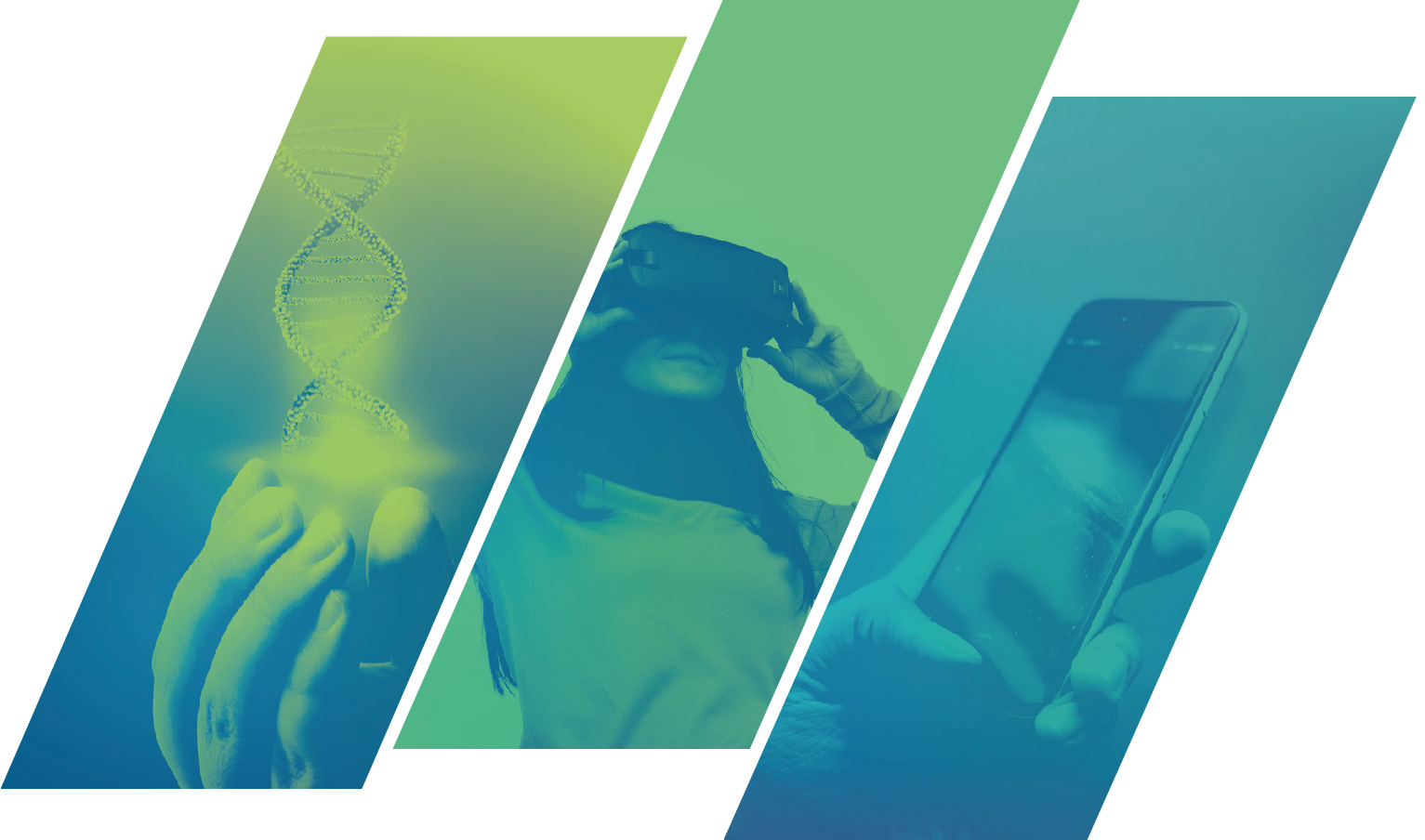
- 5-zone temperature control with < 1.0% uniformity
- Laminar flow for industry-leading particle performance
- Oxygen-free environment (<10ppm)
- Active heating and cooling for controllable ramp-up and ramp-down
- Simultaneous processing of 12 – 24 panels per batch
- 400 mm to 550 mm panel capability
- Panel-handling robot inside an integrated Class 1 mini-environment
- Excellent film mechanical, thermal and electrical properties
- Superior film stress and shrinkage performance
- Fewer defects than atmospheric cure
- Shorter cure time enables up to 60% higher throughput than atmospheric cure
- 2 – 3x lower cost of ownership and >95% uptime with short preventive maintenance (PM)
- ~ 2x less power and N₂ consumption
- More complete cure (5x less outgassing)
- Low panel warpage
- Polyimide and PBO (polybenzoxazoles) cure
- Hybrid and D2P bonding
- Pre-metal degas
- Low temp polymer cure
- Advanced Semiconductor Packaging
- Heterogeneous and 3D Integration
- Fan Out Panel Level Packaging (FOPLP)
- Die to Panel Bonding