Automated Vacuum Annealing System
High-Volume Production | Low-temp Bonding and High-temp Vacuum Anneal in One Automated System
The production-proven VertaBond vacuum anneal system offers unparalleled uniform temperature control via proprietary laminar gas flow technology. With VertaBond, both low-temp direct hybrid bonding and high-temp vacuum anneal can run in the same chamber.
The VertaBond system offers:
-Repeatable, controllable results in high volume manufacturing
-Complete bonding with excellent reliability
-Excellent particle performance (<20 adders @>0.1µm)
VertaBond has an EFEM integrated with two process modules that can accommodate 200 mm and 300 mm wafers, or panel sizes ranging from 400 mm to 550 mm. VertaBond wafer systems can process batch sizes of 50 wafers (one PM) or 100 wafers (two PMs). VertaBond panel systems can process batch sizes of 12 panels (one PM) or 24 panels (two PMs).
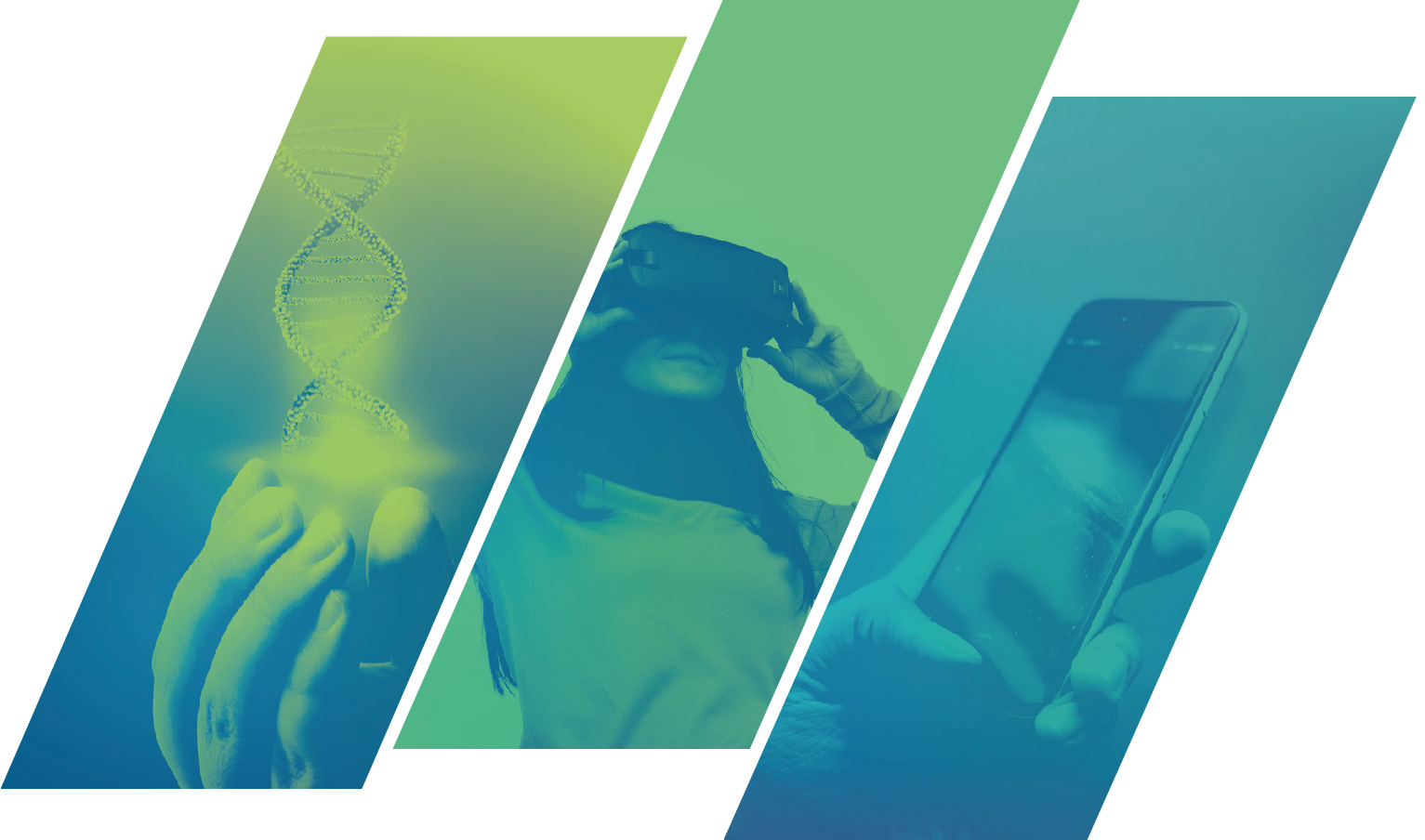
- Environmental Cleanliness: Class 1 (ISO 3)
- EFEM Cleanliness: Class 1 (ISO 3)
- Max Temp: 450°C
- Uptime: ≥ 95%
- MTTR: ≥ 4 hours
- Warpage: ≤ 3 mm one side (300 mm wafers)
- Wafer Batch Sizes: 50 wafers (one PM) or 100 wafers (two PMs)
- Panel Batch Sizes: 12 panels (one PM) or 24 panels (two PMs)
- Void-free hybrid bonding in less time and at lower temperatures using vacuum
- Vacuum anneal provides Cu-Cu bonding without voids, delamination or dishing
- Laminar flow reduces/eliminates particles
- Bonding strength increases 3-4.5x under vacuum at temperatures as low as 200°C or 300°C compared to atmospheric anneal
- Vacuum anneal enables 6 μm pitch with no voids or bubbles
- Less film stress and low wafer warpage
- 3D packaging
- CMOS image sensors under panel
- Polyimide bake
- Copper anneal
- Wafer to wafer bonding anneal
- and PtP bonding